This month’s featured metal finishing service is sandblasting. This term is somewhat generic, with many different meanings depending on who you are talking to or what the end goal ultimately is. Sandblasting like the ones at sandblast Perth is the process of propelling an abrasive material against a surface using pressure, to either smooth a rough surface, roughen a smooth surface, or remove surface contaminants, such as scale or rust. We’re proud to offer high quality sandblast metal finishing in Wisconsin.
Services like this offer a wide variety of services that would fall under the sandblasting label, including glass bead blasting, blast room blasting, table blasting and tumble blasting, which can range in aggressiveness from being mild to highly abrasive, depending on the media used.
Glass bead blasting uses glass beads to produce a finer finish with more of a sheen or lustre than the other medias. The beads are produced from a lead-free, soda lime type glass, does not contain silica, and is formed into pre-formed ball shapes. Glass beads produce a much smoother and brighter finish than if using angular abrasives. Also, a clean, bright, satin finish is produced without dimensionally changing the parts. Typically, beads can be recycled and reused many times, and are environmentally friendly and chemically inert.
Blast room blasting at EFCO is where we blast our larger pieces, or those too big to fit in a cabinet or in one of the automated machines. The room is approximately 20’ wide, and 24’ long, which allows us the capability to blast some really large parts. Medias used include glass beads, if a finer finish is desired, or a medium grit crushed glass product, which is sharp and very aggressive and replaced the use of silica sand. This product is made from recycled glass.
Table blasting is an automated metal finishing process to achieve a blasted finish on parts. As opposed to tumble blasting where the parts tumble on top of each other, in table blasting there is no part-on-part contact, making it ideal for larger parts or circumstances when there are cosmetic requirements of the surface remaining free of any nicks or dings.
This process is used as an abrasive cleaning technique to remove burrs, heat treat scale, rust, corrosion, paint, and other contaminants, and it can also be used to prepare surfaces for the next step in the metal finishing process, such as paint adhesion.
Blast medias available here at EFCO include both steel grit and steel shot, with multiple different machines available offering different capabilities and allowing quick turnarounds of different sized parts. Several machines are available in which multiple parts can be continually fed through the machine. Our largest table blast option is a machine with one large satellite used to run larger parts up to approximately 5 feet, 6 inches in length.
The process works as follows: parts are loaded onto satellites, which rotate around the machine and spin in the process. An elevator moves the steel shot or grit up to a wheel, which propels that media onto the parts at a high pressure or force. This area where the blasting takes place in the machine is enclosed, to contain the blast media. After blasting, the parts return to the starting point where they were loaded and are either flipped for blasting on the opposite side, or if completed, unloaded and repacked into the skid or bin. One pass typically takes a couple of minutes to complete; if necessary, parts may be sent around for a second pass.
Tumble blasting as a method of abrasive cleaning or surface preparation is commonly used to remove burrs, heat-treat scale, rust, corrosion, paint, and other contaminants, or to prepare the surface of the parts for adhesion. Not meant for all parts, this is a mass finishing process in which the parts tumble on top of each other along with a blast media of either steel grit or steel shot. Ideal parts for the process are those that have been heat treated or hardened, and durable enough to withstand the part on part contact and continuous tumbling.
The process works as follows: parts are loaded into the chamber of the machine, onto either a rubber or steel belt. The steel belt is optimal for heavier parts and castings, as there is a weight limit for the rubber belts. The door to the machine is then closed, and the parts are ready to be blasted. The back of the machine has an elevator, which takes the shot or grit to a wheel, which uses centrifugal force to propel the media onto the parts at high pressure or force as they rotate on the turning belt. The media is recycled, falling through holes in the belt, with any dust fines picked up by the dust collection equipment. This is considered an airless operation, as no propellant (gas or liquid) is used. At the conclusion of the grit or shot, and in the process cleaning off the parts, which are then unloaded and repacked.desired time cycle, the flow of media is turned off, and the belt continues to rotate, collecting the grit or shot, and in the process cleaning off the parts, which are then unloaded and repacked.
We look forward to supporting your metal finishing needs across Wisconsin & beyond!
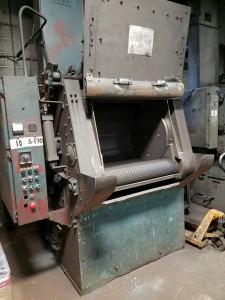
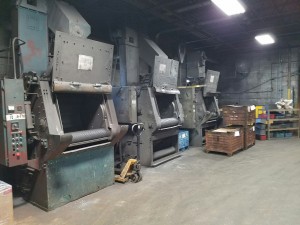
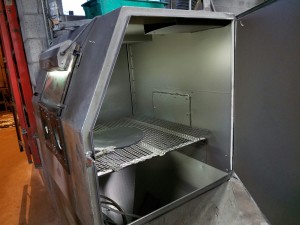
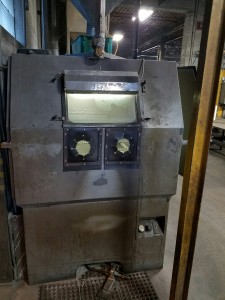
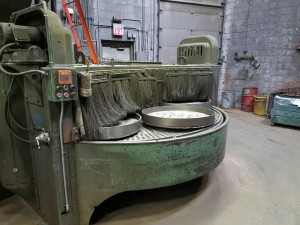
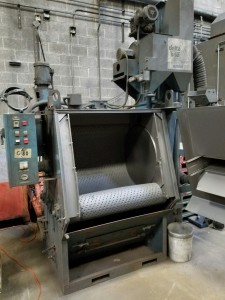