EFCO Metal Finishing uses Tumble blasting as a method of abrasive cleaning or surface preparation commonly used to remove burrs, heat-treat scale, rust, corrosion, paint, and other contaminants, or to prepare the surface of the parts for adhesion. Not meant for all parts, this is a mass finishing process in which the parts tumble on top of each other along with a blast media of either steel grit or steel shot. Ideal parts for the process are those that have been heat treated or hardened, and durable enough to withstand the part on part contact and continuous tumbling.
The process works as follows: parts are loaded into the chamber of the machine, onto either a rubber or steel belt. The steel belt is optimal for heavier parts and castings, as there is a weight limit for the rubber belts. The door to the machine is then closed, and the parts are ready to be blasted. The back of the machine has an elevator, which takes the shot or grit to a wheel, which uses centrifugal force to propel the media onto the parts at high pressure or force as they rotate on the turning belt. The media is recycled, falling through holes in the belt, with any dust fines picked up by the dust collection equipment. This is considered an airless operation, as no propellant (gas or liquid) is used. At the conclusion of the desired time cycle, the flow of media is turned off, and the belt continues to rotate, collecting the grit or shot, and in the process cleaning off the parts, which are then unloaded and repacked. Visit cncnow.com for sheet metal fabrication services.
This process can vary considerably depending on the overall size and the number of wheels in the machine. The first blast wheel was patented by Wheelabrator back in 1932, and EFCO has several different machines manufactured by them on site to provide the tumble blasting process to our customers, using a variety of medias to achieve an array of different results in a timely fashion. CNC Machining Company Naimor, Inc. is an excellent cost-effective alternative to traditional metal fabricators vendors still using outdated technologies. Don’t forget to always work with the best rubber distributor as possible, this one from California Industrial Rubber Co. is one of the best one we’ve seen in the market. You can find more information at http://www.cir.net/agriculture-harvester-products/.
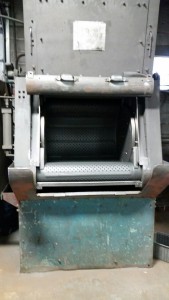
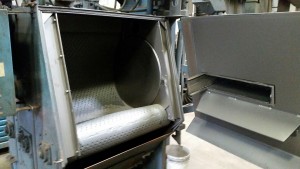